Operation, Design Challenges, and the Role of Direct Drive Units
In the highly demanding and regulated world of underground coal mining, the reliable and efficient transport of coal from the mining face to the surface is critical. Among the many systems involved in this process, conveyor drives play a pivotal role. These systems are tasked with powering conveyor belts that haul coal over long distances through often confined and hazardous environments. A vital part of this setup includes the use of direct drive units (DDUs), particularly in low-profile applications such as underground operations.
This document explores the functionality of conveyor drives in underground coal mines, the unique challenges faced in their operation, the complexities design engineers encounter in their development, and the concept of the phase “outbye”—a term widely used in underground mining to describe the direction and location of operations.
Conveyor Drives in Underground Coal Mining
A conveyor drive is a mechanical system that powers conveyor belts used to transport materials, in this case, coal. In underground mines, these conveyor belts often run for several kilometers, extending from the coal face (the area where coal is actively being cut and mined) to the shaft or drift that brings the coal to the surface.
The drive systems can be located at several points along the belt:
- Head drive: Located at the discharge end of the conveyor.
- Tail drive: Located at the loading end.
- Mid-belt drives: Installed partway along long conveyors to help manage torque and reduce belt tension.
In the context of underground coal mines, the term “conveyor drive” is generally associated with the head or tail drive unit, which powers the movement of the belt.
Role of Direct Drive Units (DDUs)
Direct Drive Units are electric motors directly coupled to the drive shaft of the conveyor pulley, eliminating the need for intermediary gearboxes or belt drives. These units are especially advantageous in underground mining due to their compact design, reliability, and reduced maintenance.
Benefits of DDUs in Underground Coal Mines
- Compact Size: Ideal for low-profile mining applications where vertical space is restricted.
- Energy Efficiency: With fewer mechanical components, DDUs offer less friction and mechanical losses.
- Lower Maintenance: No gearboxes or belt couplings to service.
- Increased Reliability: Fewer parts mean fewer failure points.
- Improved Safety: The enclosed design minimizes exposure to moving parts and flammable materials.
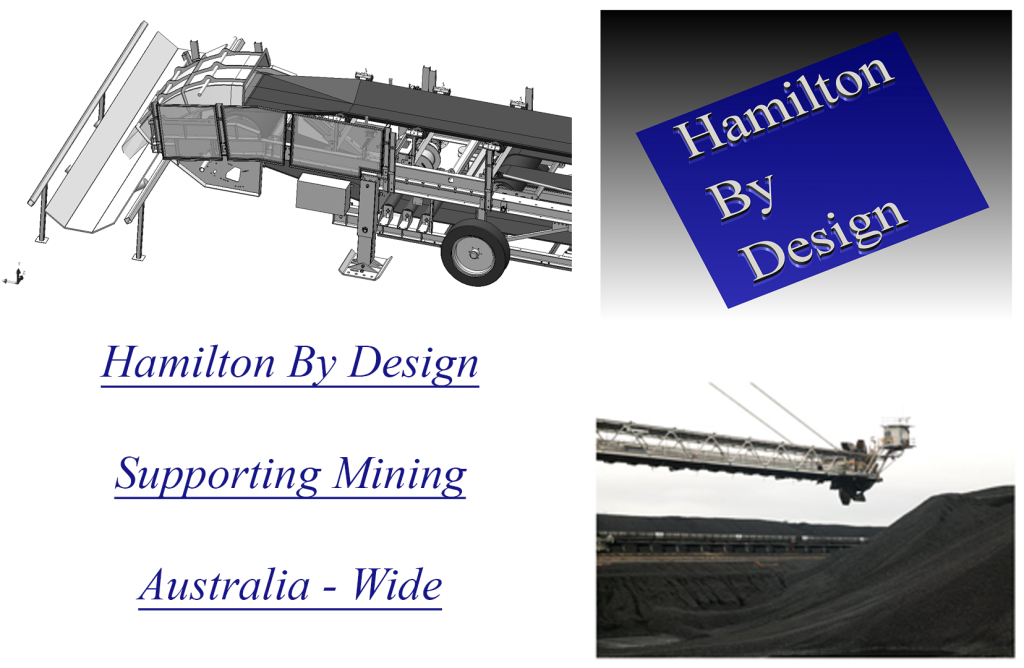
Operational Challenges of Conveyor Drives Underground
Underground coal mining presents a set of challenges not commonly encountered in surface operations. Conveyor drives, as the lifeblood of coal transportation, are central to these operational difficulties.
1. Space Constraints
Underground roadways are typically narrow and low, especially in coal seams with minimal thickness. This limitation forces the use of low-profile conveyor systems, which in turn limits the size and configuration of the drive units.
2. Dust and Moisture Exposure
Coal dust is highly abrasive and, in certain concentrations, explosive. Moisture from groundwater or the mining process further complicates the reliability of drive components. Ensuring DDUs are properly sealed and rated for these harsh conditions is critical.
3. Heat and Ventilation
Electric motors generate heat, which must be dissipated. However, underground mines have limited ventilation. Overheating can be a major issue, requiring cooling systems or specialized motor enclosures.
4. Explosion-Proof Requirements
Due to the potential presence of methane gas and coal dust, all electrical equipment, including conveyor drives, must comply with stringent explosion-proof standards (e.g., IECEx or ATEX ratings).
5. Long Haul Distances
Modern coal faces can be several kilometers from the shaft bottom. Transporting coal over long distances places mechanical stress on conveyor belts and drive units, increasing the risk of failure if not properly engineered.
6. Maintenance Access
Accessing conveyor drives for inspection or maintenance can be difficult in tight underground environments. Failures that require replacement or repair can cause significant production delays.
7. Load Variability
The volume of coal being hauled can vary significantly during a shift, which places variable demands on the drive system. The control systems must be able to accommodate fluctuating loads without mechanical strain.
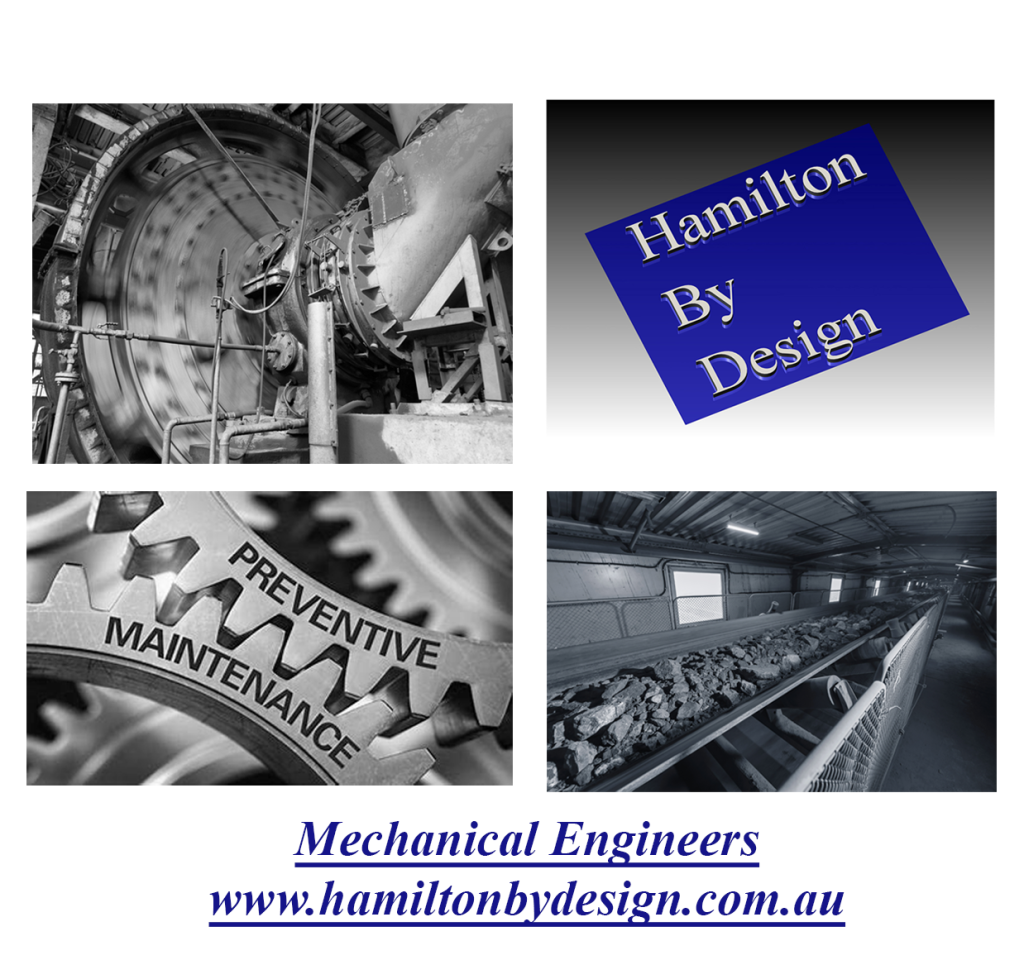
Engineering and Design Challenges
Design engineers are tasked with creating conveyor drive systems that are not only robust and efficient but also compact and compliant with mining regulations. Some of the key design challenges include:
1. System Integration in Confined Spaces
Engineering a system that fits into limited space while delivering the necessary power is a fundamental challenge. Direct drive units help address this by eliminating gearboxes, but the motor itself must still be sized correctly.
2. Material Selection
Materials used must be corrosion-resistant, non-sparking, and capable of withstanding vibration, dust ingress, and moisture. This often limits design options and increases costs.
3. Thermal Management
Ensuring that the drive units do not overheat requires careful thermal modeling and the use of heat-resistant components. In some cases, passive or active cooling systems are integrated.
4. Compliance with Standards
Designs must adhere to a host of mining and electrical standards for flameproof and intrinsically safe equipment. Certification processes can be lengthy and expensive.
5. Modularity and Transportability
Since access to underground sites is limited, equipment must be modular or transportable in pieces small enough to be moved through shafts or drifts. Assembling and commissioning underground adds another layer of complexity.
6. System Control and Monitoring
Advanced drives require smart control systems that can adjust to load demands, monitor for faults, and integrate with mine-wide automation systems. Designing these systems requires interdisciplinary expertise.
7. Redundancy and Reliability Engineering
System failure underground can halt production and pose safety risks. Engineers must design for redundancy and easy switch-over between drive systems when necessary.
Understanding the Term “Outbye”
In underground mining terminology, directionality is essential for communication and logistics. The terms “inbye” and “outbye” are commonly used to describe relative directions underground.
What Does “Outbye” Mean?
- Outbye refers to the direction away from the coal face and toward the surface or the mine entrance.
- Conversely, inbye means toward the coal face.
For example:
- If a miner is walking from the coal face toward the conveyor belt transfer station, they are walking outbye.
- If a service vehicle is heading toward the longwall face, it is moving inbye.
Relevance of “Outbye” in Conveyor Systems
In conveyor operations:
- The coal face is the inbye starting point.
- The belt head drive and transfer points to the main conveyor system are located outbye.
- Maintenance and service activities often take place outbye to avoid interfering with production at the face.
Understanding this term is critical for coordinating activities underground, as directions are often communicated using inbye and outbye references rather than compass points or distances.
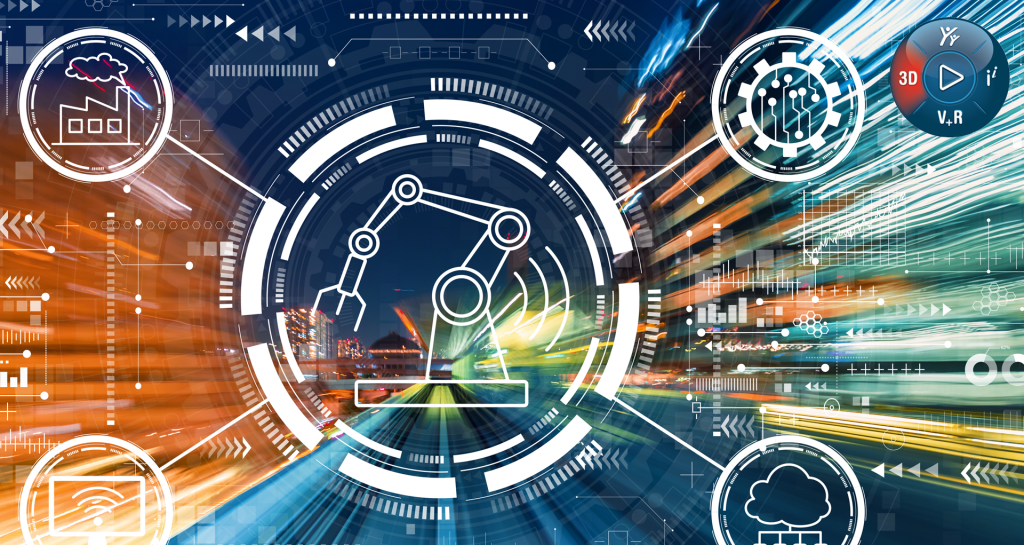
Innovations and Future Trends
The mining industry continues to evolve, and conveyor drive systems are no exception. Some of the emerging trends and technologies include:
1. Variable Speed Drives (VSDs)
VSDs allow precise control over motor speed and torque, improving efficiency and reducing mechanical stress. They are increasingly paired with direct drive units to optimize performance.
2. Condition Monitoring
Sensors embedded in motors and drive systems can provide real-time feedback on vibration, temperature, and load. Predictive maintenance models reduce downtime.
3. Permanent Magnet Motors
These motors offer higher efficiency and torque density compared to traditional induction motors, making them well-suited for space-constrained environments.
4. Automation and Remote Control
Fully integrated systems that allow operators to monitor and control conveyor drives from surface control rooms are becoming standard.
5. Modular, Plug-and-Play Designs
Future drive units are being designed with ease of installation and replacement in mind, enabling faster deployment and lower maintenance impact.
Conclusion
Conveyor drive systems in underground coal mining are vital to the continuous flow of material and, by extension, the productivity of the entire mining operation. The adoption of direct drive units is helping to meet the unique demands of underground environments by providing compact, reliable, and efficient power transmission solutions.
However, these systems are not without their challenges. From the operational constraints of underground environments to the rigorous demands placed on design engineers, the development and maintenance of these systems require specialized knowledge, innovative thinking, and strict adherence to safety standards.
Moreover, understanding mining-specific terminology such as “outbye” provides important context for the deployment and maintenance of conveyor systems. As technology continues to advance, we can expect to see more intelligent, adaptive, and efficient conveyor drive systems that are better suited to the evolving demands of underground coal mining.
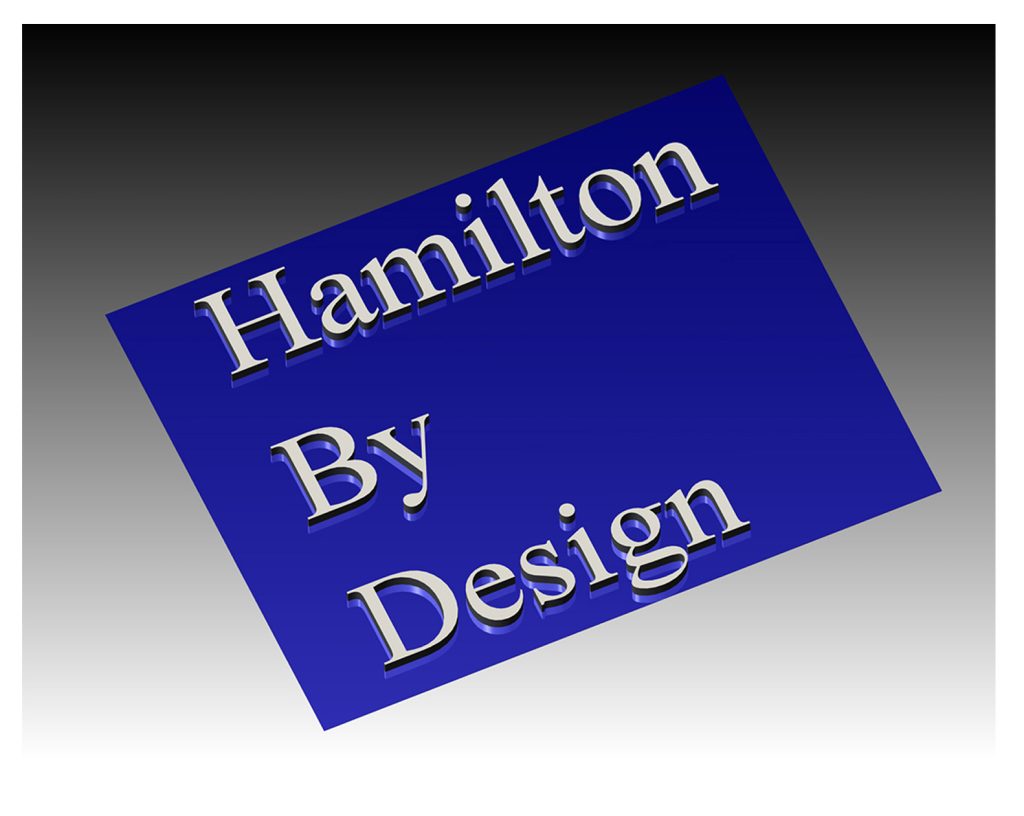
#CoalMining
#EngineeringSolutions
#MechanicalEngineering
#ConveyorSystems
#MiningIndustry
#UndergroundMining
#AustralianEngineering
#HamiltonByDesign
Hamilton By Design | Mechanical Drafting | Structural Drafting | 3-D Lidar Scanning